There are six (6) implementable clauses within ISO 9001:2015 Quality Management System Standard.
Within this series of posts over the next six weeks we will discuss the requirements to all six clauses and the correct interpretation thereof.

CLAUSE 7
7.0 Support
7.1 Resources
There requirements in Clause 7.1 are comparable to ISO 9001:2008 Clause 6.0 – Resource Management, Clause 6.1 – Provision of Resources, Clause 6.3 – Infrastructure and Clause 6.4 – Work Environment.
7.1.1 General
You should seek and record evidence conforming that your organization has considered the need for external resources in addition to the need for internal resources. Most organizations determine resource requirements during management review meetings; you should review the management review minutes for evidence of resource allocation.
7.1.2 People
You should seek and record evidence to confirm that your organization has provided the staff necessary for the effective implementation of the QMS and for the operation and control of its processes.
7.1.3 Infrastructure
You should seek and record evidence to confirm that your organization has provided the infrastructure necessary for the effective implementation of the QMS and for the operation and control of its processes.
7.1.4 Environment for the operation of processes
You should seek and record evidence to confirm that your organization has identified, provided and maintained the infrastructure necessary for achieving product conformance.
7.1.5 Monitoring and Measuring
This requirement is comparable to ISO 9001:2008 Clause 7.6 – Control of Monitoring and Measuring Equipment. You should seek and record evidence to confirm that where measurement traceability is a requirement that instruments used for measurement are subject to the following controls:
1. Devices are calibrated at intervals or prior to use, based on recognized standards;
2. Devices are adjusted as necessary in accordance with manufacturer’s instructions;
3. Devices are identified to enable calibration status to be determined;
4. Devices are safeguarded from adjustment, which may invalidate results;
5. Devices are protected from damage during handling, maintenance or storage;
6. The validity of results from a non-confirming device are re-checked with a conforming device;
7. Devices are calibrated by external providers certified to ISO 17025;
8. Records of calibration and verification are maintained;
9. Computer software which is used for monitoring/measuring is validated prior to initial use;
10. Computer software used for monitoring and measuring is re-validated where necessary;
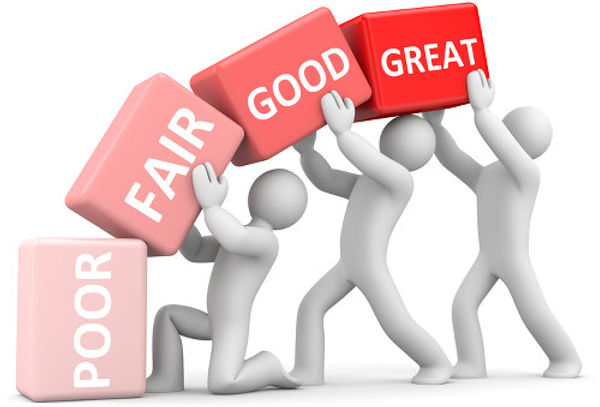
If measurement traceability is not required, verify that those monitoring and measuring resources used by your organization are suitable. You should ensure that documented information is maintained in order to demonstrate suitability of monitoring and measuring equipment.
7.1.6 Organizational Knowledge
‘Organizational Knowledge’ is a new requirement. You should seek and record evidence that your organization has taken steps to identify the internal and external knowledge necessary to ensure the continued product conformity.
Check that organizational knowledge is communicated as necessary and that it is maintained and retained in accordance with Clause 7.5. Check that organizational knowledge is reviewed before changes to QMS are made in when responding to change.
Sources of internal knowledge often include the organization’s intellectual property; knowledge gained from experience; lessons learned from failures and successes; capturing and sharing undocumented knowledge and experience; the results of improvements in processes, products and services. Sources of external knowledge often include other ISO standards; research papers; conferences; or knowledge gathered from customers or external parties.
You should seek to evidence to confirm how your organization has determined and made available the knowledge needed to keep up to date with changing situations and knowledge related to new products and services. You determine whether your organization has considered internal and external sources, such as:
1. Lesson learnt from non-conformities and corrective actions, near miss situations and successes;
2. Gathering knowledge from customers, suppliers and partners;
3. Capturing knowledge that exists within the organization, e.g. through mentoring, succession planning;
4. Benchmarking against competitors;
5. Sharing organizational knowledge with relevant interested parties to ensure sustainability of the organization;
6. Updating the necessary organizational knowledge based on the results of improvement;
7. Knowledge from conferences, attending trade fairs, networking seminars, or other external events.
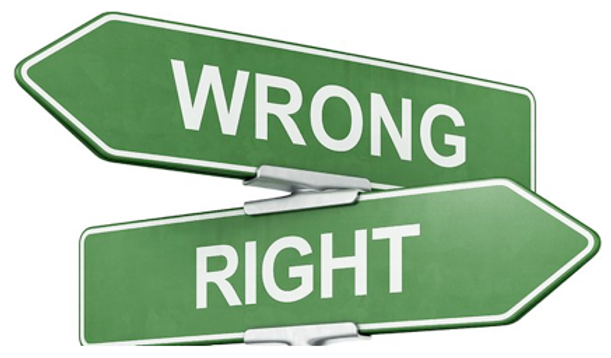
7.2 Competence
This requirement is comparable to ISO 9001:2008 Clause 6.2.1 – Human Resources and Clause 6.2.2 – Competence, training and awareness but additionally, you should check whether your organization takes action to address competency issues whilst checking that they were effective.
Your organization should establish a process for assessing existing staff competencies against changing business needs and prevailing trends. Check for evidence that all staff which work under your organization’s control are competent, and that evidence continuing competence is maintained as documented information in accordance Clause 7.5.
7.3 Awareness
This requirement is comparable to ISO 9001:2008 Clause 6.2.2 – Competence, training and awareness which was limited to the organization’s own personnel. You seek evidence to confirm that this requirement has been applied by your organization to ensure that the people who need to be made aware now include all the people who work on your organization’s behalf that affect the conformity of your organization’s QMS or products. You ensure that these people are aware of:
1. The quality policy;
2. Relevant quality objectives;
3. Their contribution to the effectiveness of the quality management system, including the benefits of improved performance;
4. New requirement. The implications of not conforming to the quality management system requirements.
The awareness training does not need to follow the format of long classroom sessions. Training techniques can include short training segments supplemented with videos and hands-on demonstrations that address key elements of the QMS.
Other methods to promote and reinforce the environmental awareness training sessions include communication via electronic bulletin boards, posters, newsletters and informational meetings.
7.4 Communication
This requirement is comparable to ISO 9001:2008 Clause 5.5.3 – Communication but it now includes the new requirement to also communicate with external parties, e.g. those previously defined in Clause 4.2. You should seek evidence to confirm that your organization has identified the necessary internal and external communications that are required for the operation of the QMS. You should confirm how your organization has determined:
1. What it needs to communicate;
2. When it will communicate;
3. With whom it will communicate;
4. How it will communicate.
Internal Communications
All well as briefing employees during introductory presentations, try using a combination of other methods to promote awareness, such as posters placed on notice boards and leaflets with pay-slips, etc. Use training sessions to inform employees of the plan, how they will be expected to contribute. Issues pertaining to the quality management system that could be communicated include:
Day-to-day operations and general awareness;
Information on achieving objectives and targets;
Risk and opportunities.
Auditors will wish to determine if the policies meet the intent and are understood, by interviewing personnel at all levels. Although the exact content of the policies does not need to be recited by interviewees, the awareness of the policies and how their job affects the company objectives should be determined. This does not require your employees to memorize the policies but it does mean they should be aware of it, know where it may be found and be able to paraphrase, or give an interpretation as it applies to them.

If the personnel interviewed do not know what their measurable objectives are and/or do not know what the organizational objectives are that they have a direct effect upon, the auditor would be further directed to evaluate top management’s communication of the policies and objectives.
Inferred awareness through knowledge of procedures is not considered sufficient; otherwise why have the requirement in the first place? A quick and convenient way to promote and communicate the policy might be to create a shortened version of main policy; try condensing it to five key words or even a couple of short sentences. This can be posted on bulletin boards in each department.
You could even add it to the reverse side of staff security passes or ID badges. If an auditor asks an employee whether they are aware of the policy; they can point to the bulletin board, or point to it on their badge. The employee can further elaborate to the auditor, what the policy means to them and how it influences their work.
External Communications
In most instances, external interested parties (such as consumers, stockholders, neighboring communities, etc.) are the main driving forces for organizations to implement a QMS. The appropriate external communications may establish environmental and safety credibility and satisfy stakeholder requests by presenting objective information on the organization’s significant aspects, its QMS, or its performance. The various processes or means of external communication may include:
Annual reports or newsletters of performance sent to external stakeholders;
Open house meetings for interested parties and focus groups;
Availability of regulatory submissions, or results of audits;
Policies published in the media and industry association publications and press releases;
The various means of such communication are endless. Such communication may benefit your organization in several ways, including improved employee morale and increased market exposure, either of which can lead to increased profits.
Join our mailing list to receive upcoming posts: http://www.isoqar.co.za/