There are six (6) implementable clauses within ISO 9001:2015 Quality Management System Standard.
Within this series of posts over the next six weeks we will discuss the requirements to all six clauses and the correct interpretation thereof.

10.3 Continual Improvement
This requirement is comparable to ISO 9001:2008 Clause 8.5.1 Continual Improvement. One of the driving goals of ISO 9001 is the principle of continual improvement. You must be able to demonstrate continual improvement. Most auditors would expect you to revise the quality system documentation and processes as the quality management system matures or when a new process is implemented.
You should seek objective that your organization has implemented a process, with appropriate methods, techniques, and formats for identifying areas of underperformance or opportunities for improvement. You should expect to evidence that your organization has selected the appropriate tools and techniques to investigate the causes and thereby establishing and implementing a process for continual improvement. The impetus for continual improvement must come from the use of (as a minimum):
1. Quality policy (Clause 5.2);
2. Risks and opportunities (Clause 6.1);
3. Quality objectives (Clause 6.2);
4. Analysis and evaluation of data (Clause 9.1);
5. Audit results (Clause 9.2);
6. Management review (Clause 9.3).
7. Non-conformity and corrective action (Clause 10.2);
Requirements for continual improvement interrelate with the following clauses:
2. Quality objectives (Clause 6.2);
3. Risks and opportunities (Clause 6.1);
4. Recommendations for improvement (Clause 9.3.2);
5. Improvement of the system, processes and product(Clause 9.3.3);
6. Analysis and evaluation of data (Clause 9.1);
7. Non-conformity and corrective action (Clause 10.2);
It is the responsibility of the company to demonstrate improvement rather than the auditor to look for it. Accordingly, it is a useful audit practice to ask management to identify any improvement initiatives taken since the previous visit, and also any planned for the future.
Processes can always be made more efficient and effective, even when they are producing conforming products. The aim of a continual improvement programme is to increase the odds of satisfying customers by identifying areas that need improvement. It requires the organization to plan improvement systems and to take into account many other activities that can be used in the improvement process.
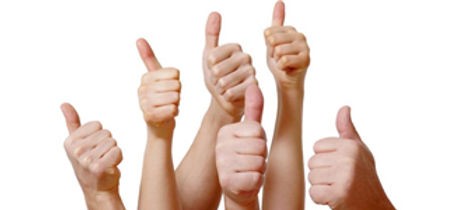
You will be required to ensure that you continually improve the degree to which your products and services meet customer requirements and to measure effectiveness of your processes. To this end the continual improvement principle implies that you should adopt the attitude that improvement is always possible and your organizations should develop the skills and tools necessary to drive improvement.
The PDCA cycle is a perfect way of introducing continual improvement to your organization’s activities. Each step to improvement can be defined by four sub steps, Plan, Do, Check and Act:
1. Plan: Establish a timetable for internal audits and management reviews. Establish the objectives and processes necessary to deliver results in accordance with your customer’s requirements and your organization’s policy.
2. Do: Implement changes designed to solve the problems on a small scale first to see the effect. This minimizes disruption to routine activity while testing whether the changes will work or not.
3. Check: Monitor and measure processes and product against policies, objectives and requirements and report the results. Also check on key activities to ensure that the quality of the output is conforming and not influenced by the changes.
4. Act: Take actions to continually improve process performance. Implement the changes on a larger scale, if the experimental changes have proven to be successful. This means making the changes a routine part of the activity.
Also act to involve other people, departments or suppliers affected by the changes and whose co-operation is needed to implement them on a larger scale. Make sure that changes are documented properly according to the documentation requirements.
Join our mailing list to receive upcoming posts: http://www.isoqar.co.za/