There are six (6) implementable clauses within ISO 45001:2018
Occupational Health and Safety Management Standard.
Within this series of posts over the next six weeks we will discuss the requirements to all six clauses and the correct interpretation thereof.
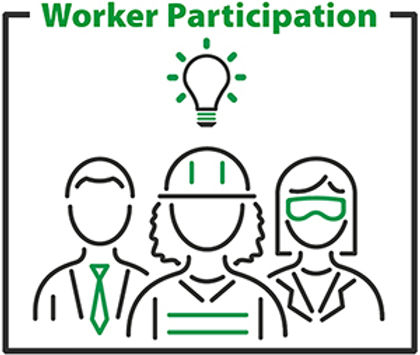
Clause 5: Leadership and worker participation Top management in ISO 45001 is responsible and accountable for the prevention of work-related injury and ill health as well as the provision of safe and healthy workplaces. It should also be noted that leadership and culture are identified as potential hazards later in the standard (6.1.2.1a). Top management must ensure that a process for consultation and participation with workers is established. It is also top management’s responsibility to establish, implement, and maintain the health and safety policy. The required contents for the policy include elements such as a commitment to consultation and participation of workers. Consultation and participation of workers (including non-managerial workers) is significantly enhanced from OSHAS 18001, which was limited to participation in hazard identification and consultation on changes. In ISO 45001 the organization is now required to provide the mechanisms, time, training, and resources for consultation and participation of workers. This includes removing any barriers such as language, literacy, or fear of reprisals.
5.1: Leadership and commitment
Leadership, commitment and active support from top management are critical for the success of the OH&S management system and for the achievement of its intended outcomes.
Top management establishes an organization’s mission, vision and values, considering its context, the needs and expectations of its relevant interested parties, and business objectives. These are reflected in its strategic business plans. Top management’s leadership and commitment are vital for the successful implementation of an effective OH&S management system. Therefore, top management must take responsibility for the effectiveness of the organization’s OH&S management system and ensure that its intended outcomes are achieved.
If workers observe top management taking OH&S responsibility seriously this will greatly assist in the establishment of a positive OH&S culture throughout the organization.
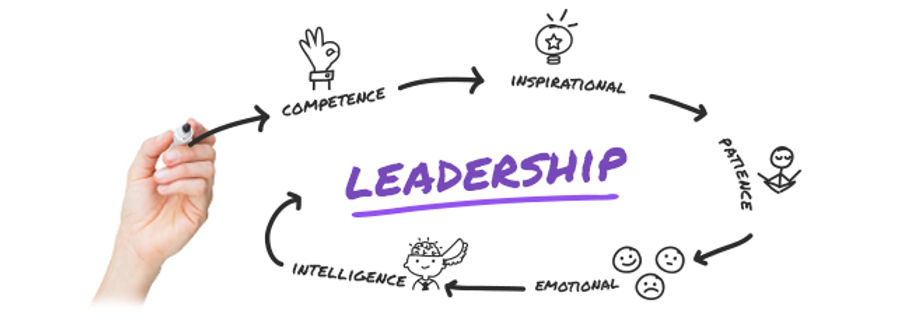
Leadership and commitment can be shown by, means of:
- Aligning the OH&S management system with the organization’s business objectives;
- Ensuring the necessary resources are available;
- Encouraging workers and other relevant interested parties to get actively involved in improving OH&S performance;
- Involving everyone in OH&S decision-making that affects them;
- Promoting open discussion about OH&S matters.
The organization can improve the OH&S culture, by:
- Providing clear and consistent leadership;
- Promoting formal and informal involvement of workers;
- Making sure controls are practical and proportionate to the risks;
Top management should communicate the importance of effective OH&S management and conformance to OH&S management system requirements by direct involvement or through delegation of authority, as appropriate. This communication can be formal or informal.
Top management should support others in the organization in relevant managerial roles so that they in turn can demonstrate leadership in their own area of responsibility. By this means, top management’s leadership and commitment cascades down through the organization. By demonstrating leadership and commitment, top management can direct and support employees of the organization and others doing work on its behalf to achieve the intended outcomes for its OH&S management system.
The organization is in a better position to achieve its OH&S objectives and to identify opportunities for improvement when top management creates a culture that encourages people, at all levels, to actively participate in the OH&S management system.
5.2: OH&S policy
The OH&S policy is the mechanism by which top management formally articulates its commitment to OH&S probity.
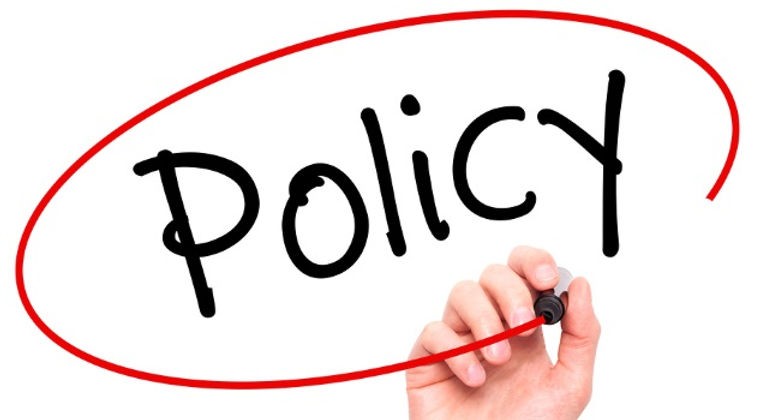
At a minimum, these commitments are required:
Provide safe and healthy working conditions for the prevention of work-related injury and ill health which are appropriate to the specific nature of the OH&S risks to which workers and others are exposed;
- Provide a framework for setting the OH&S objectives;
- Include a commitment to fulfill legal and other requirements;
- Include a commitment to eliminate hazards and reduce OH&S risks;
- Include a commitment to continual improvement of the OH&S management system;
- Include a commitment to consultation with and participation of workers, and, where they exist, workers’ representatives.
It is important to share the organization’s commitments with its workers, contractors and others who work on behalf of the organization so that they understand top managements’ expectations and can perform their work in a manner that contributes to meeting these expectations. Making the health and safety policy publicly available, or available on request, provides assurance to interested parties that the organization is doing its part to achieve positive OH&S outcomes.
The policy should take account of:
- The current OH&S circumstances of the organization and what the organization wants to achieve;
- Broader business objectives;
- Opportunities for improving the health and safety of workers.
- The OH&S policy should be reviewed periodically to ensure that it remains relevant and appropriate to the organization.
5.3: Organizational roles, responsibilities and authorities
Top management should ensure that the responsibilities and authorities for relevant roles within the OH&S management system are assigned and communicated at all levels within the organization and maintained as documented information.
Top management is ultimately responsible for the OH&S management system, even if the day-to-day decisions related to occupational health and safety are delegated to others. What is delegated and to whom should be clearly and unambiguously communicated so that everybody understands who is responsible for what.
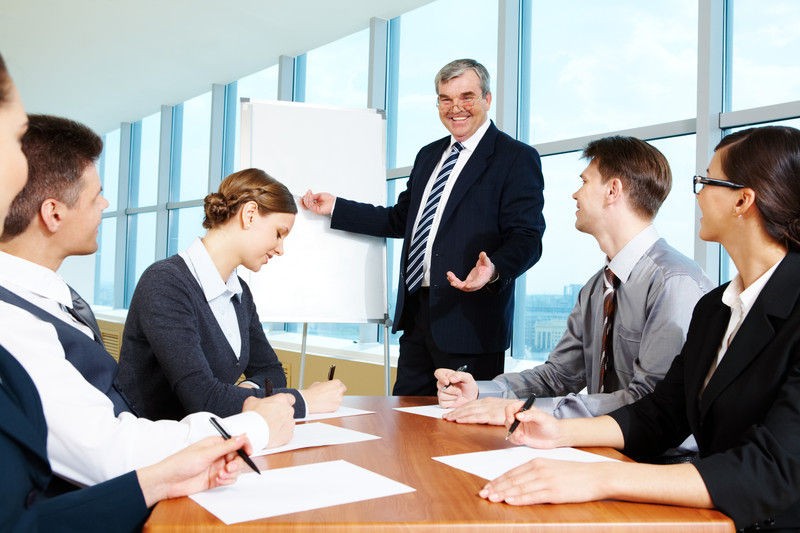
Top management should assign the responsibility and authority for:
- Ensuring that the OH&S management system conforms to the requirements of ISO 45001;
- Reporting on the performance of the OH&S management system to top management.
Since resources can be limited, opportunities should be sought out to integrate OH&S responsibilities within existing functions of the organization, such as manufacturing, facilities management, purchasing, and human resources.
If other management systems are already in place, such as quality, environment, energy or food safety, synergies may exist where there are similar roles and responsibilities. This will enhance ownership of OH&S management across the organization and potentially create efficiencies.
ISO 45001 requires that the responsibilities and authority of all persons who perform duties that are part of the OH&S management system be documented. These can be described and included in:
- OH&S management system procedures;
- Operational procedures and process maps;
- Project and/or task descriptions;
- Job descriptions;
- Induction training packages.
Such documentation can, among others, be required for the following personnel:
Management at all levels in the organization, including top management;
- Safety committees/safety teams;
- Process operators and the general workforce;
- Those managing contractors;
- Those responsible for OH&S training;
- Those responsible for equipment operation and maintenance;
- Those responsible for facilities management;
- Employees with OH&S qualifications, or other OH&S specialists, within the organization;
Care should be taken with the clarification of responsibilities at the interfaces between different functions (e.g. between departments, between different levels of management, between workers, between the organization and contractors and between the organization and its neighbors).
5.4: Consultation and participation of workers
Involvement of workers in the OH&S management system and the processes that support it is a key requirement of effective OH&S management as it enables the organization to make informed decisions.
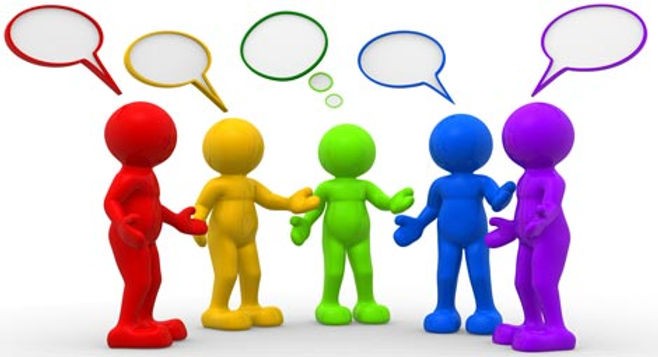
There is an onus on the organization to:
- Provide processes, time, training and resources deemed necessary for consultation and participation;
- Provide, in a timely manner, access to clear, understandable and relevant information about the OH&S management system;
- Identify and remove obstacles to participation such as failure to respond to worker suggestions, language or literacy difficulties, policies that discourage worker participation, and minimize those that cannot be removed;
- Encourage consultation with non-managerial workers relating to a range of OH&S issues;
- Encourage the participation of non-managerial workers in a range of OH&S activities and decisions.
It is up to the organization to determine the best way of ensuring effective consultation and participation and whether it needs to set up formal mechanisms such as health and safety committees. While consultation is about seeking workers’ views, and considering them, before making a decision, participation is about joint decision-making, e.g. jointly undertaking a risk assessment and agreeing actions or being involved in deciding the organization’s OH&S policy and objectives.
For small organizations it can be effective to include all workers in discussions and decision-making, whilst in larger organizations, it can be more effective to appoint one or more workers’ representatives. Other mechanisms for consultation and participation include focused team meetings, workshops, worker surveys and suggestion schemes.
The organization should ensure that processes for consultation and participation of workers include contractors and other interested parties, e.g. people working in parts of the organization not covered by the management system, carrying out work under the organization’s control, where relevant. This can include, for example, consultation with contractors on issues such as dealing with hazards which might be new or unfamiliar to them.
Typical of the activities that workers can participate in include the following:
- Identifying hazards and assessing risks and opportunities;
- Determining actions to eliminate hazards and reduce OH&S risks;
- Determining competence requirements and conducting training needs analysis;
- Determining what needs to be communicated and how this will be done;
- Determining control measures and their effective implementation and use;
- Investigating incidents and nonconformities and determining corrective actions;
- Developing and reviewing of OH&S policies and objectives;
- Developing new or improved OH&S arrangements and procedures.
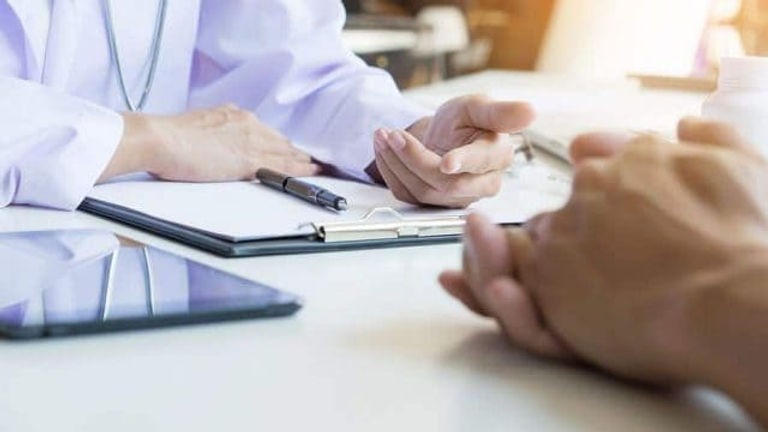
In considering the need for consultation, the organization should take account of the following:
- New or unfamiliar hazards (including those that might be introduced by contractors);
- Reorganization;
- New processes, procedures or work patterns;
- The construction, modification or change of use of buildings and facilities;
- The introduction of new or modified equipment;
- New or amended controls;
- The use of new chemicals or materials;Changes in emergency arrangements;
- Changes in legal and/or other requirements;
Topics for consultation include:
- Determining the needs and expectations of interested parties;
- Establishing the OH&S policy;
- Assigning organizational roles, responsibilities and authorities as applicable;
- Determining how to fulfill legal and other requirements;
- Establishing OH&S objectives and planning to achieve them;
- Determining applicable controls for outsourcing, procurement and contractors;
- Determining what needs to be monitored, measured and evaluated;
- Planning, establishing, implementing and maintaining an audit programme;
- Ensuring continual improvement.
The organization should encourage active and ongoing participation of and consultation with workers in the development and review of OH&S practices and, where appropriate, the development of the OH&S management system. The participation arrangements should take account of any legal and other requirements.
Join our mailing list to receive upcoming posts: http://www.isoqar.co.za/