There are six (6) implementable clauses within ISO 9001:2015 Quality Management System Standard.
Within this series of posts over the next six weeks we will discuss the requirements to all six clauses and the correct interpretation thereof.
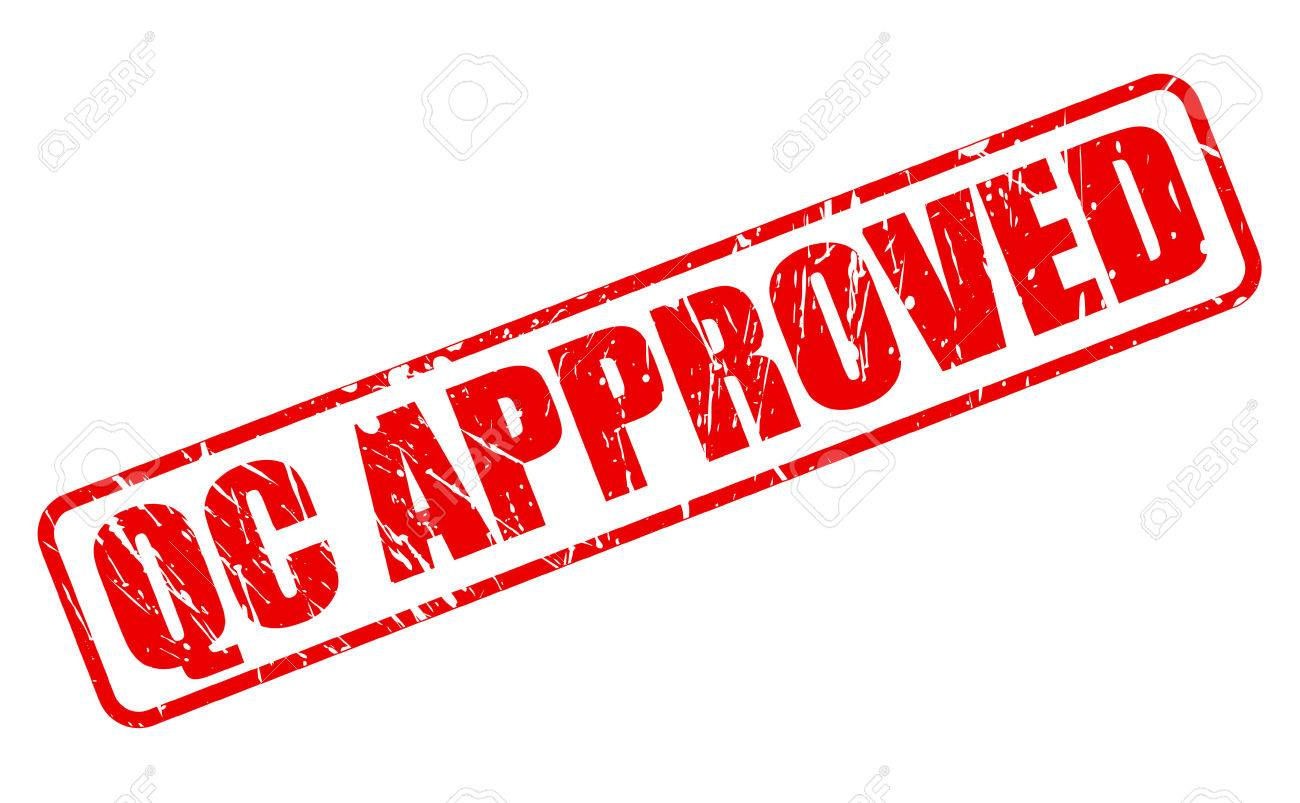
8.0 Operation
8.6 Release of Products and Services
This requirement is comparable to ISO 9001:2008 Clause 8.2.4 Monitoring and Measurement of Processes. Your organization must show evidence that a process (method, techniques, formats, etc.) is in place to monitor and measure the characteristics of product to verify that requirements are being met. This must be accomplished at appropriate stages of the design and development process. The auditor will verify that records are maintained to provide evidence of conformity and indicate the person(s) authorizing the release of products.
The release of product or delivery of service must not be completed until the planned requirements (7.1) have been met. ‘Release’ of product may include, according to product planning and the verification stages, release to the next operation, release to an internal customer, release to final customer, etc.
For product release or service delivery, the planning requirements may be waived, but must be approved by relevant authority and by the customer as appropriate. Monitor and measure product characteristics to ensure they are able to demonstrate:
1. Product characteristics are continually met;
2. Evidence of conformity with product requirements.

8.7 Non-conforming Process Outputs, Products & Services
This requirement is comparable to the requirements from ISO 9001:2008 Clause 8.3 – Control of Non-conforming Product but it now includes as a new requirement, the terms ‘process outputs’ and ‘services’ as well as products. It should be noted that there is no need to maintain a documented procedure but your organization may still chose to operate one. You should seek and record evidence that your organization has retained documented information concerning non-conformities and the actions arising.
Controlling Product and Process Non-conformities
No matter how you resolve a non-conformance, you must keep records of each non-conformance and how it was dealt with. Records of product non-conformity should be periodically reviewed to determine if a chronic problem exists with the production process, it’s all about improvement!
By keeping records of your non-conformities it is easier to spot negative trends and examine the root cause, and eliminate the cause of your problems. This, in turn, should result in fewer defective products or process outputs and could lead to more satisfied customers.
If you have manufactured a product, inspected it and found it to be out of specification, it is most likely to be deemed nonconforming product. In some instances you will have to scrap the defective product but in other situations you may be able to do some remedial work and bring it back into specification.
What the clause is telling us is that the product should then be subject to further inspection to verify that it is now correct. As for records, if you documented the non-conforming product there should normally be somewhere to verify that you successfully (or not) cured the problem and that it is now conforming.
Re-verification simply means that you cannot assume that because someone tells you they have corrected the problem then it is ok. The clause is asking you to re-verify by whatever means you originally chose. If you used inspection as a method of verification then re-inspect in the same method. If not, use whatever method suits you (or your customer). Just make sure it is ok before it leaves!
The re-verification after remedial work might involve testing as well as inspection. The reason is not just to verify that the defect has been removed, but also to assure that fresh defects have not been introduced by the rework.
Records would be as appropriate for the re-inspection or re-testing performed. Re-verification is equivalent to re-inspection and records could include a signature of approval or a more formal test report. Whichever format is chosen, it must defined Control of Non-conformance procedure.
Generally, you could take two routes. If you have an internal non-conformance then depending on your NCR documentation, your verification could be documented on your non-conformance report. If your non-conformance is external, you should supply evidence of conformance to your customer.
You may need to supply new evidence of conformance to your customer along with corrective action documentation if requested. The method that you use in either of these situations should be defined in your IMS and procedures, that way you relieve yourself and your auditor from guessing how you would address them.
Where necessary, any product or process outputs that do not conform to specified requirements should be properly identified and controlled to prevent unintended use or delivery. Improvements are then implemented to ensure the non-conformance does not reoccur. Control non-conforming products by:
1. Defining how non-conforming products and processes are identified;
2. Defining how non-conforming products and processes are dealt with;
3. Removing or correcting non-conformities;
4. Preventing the delivery or use of non-conforming products and processes;
5. Verifying how non-conforming products and processes were corrected;
6. Providing evidence that corrected products and processes now conform to requirements;
7. Keeping records that catalogue non-conforming products and processes.
Controlling non-conformances applies to services just as much as it does to tangible goods. Reports, data, test results and intellectual property, to name just a few service outputs, can all be potentially non-conforming, in which case all the disciplines of this process apply. It is the company’s policy is to detect, control and rectify any aspect of non-conformance as quickly and efficiently as possible.
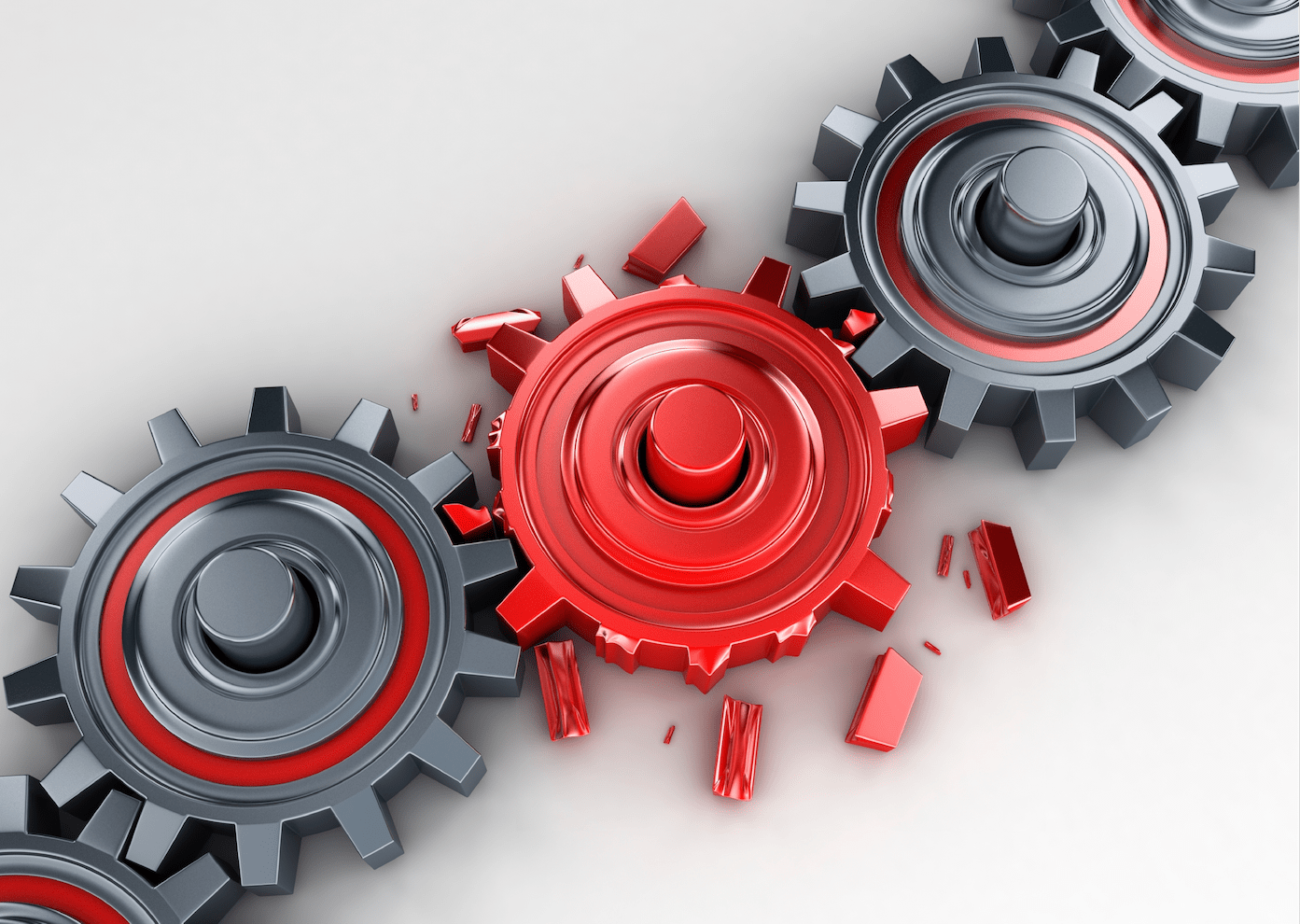
Controlling Service-based Non-conformities
In the case of service processes that directly involve the customer, the control of non-conforming outputs is the way the organization deals with non-conformities in the service provision until the appropriate corrective action can be defined and implemented. When non-conformities are identified, you should examine whether the personnel involved are sufficiently empowered with the authority to decide the disposition of the service, for example:
1. To immediately terminate the service;
2. To replace the service provided;
3. To offer an alternative.
You should also examine:
1. Your organization’s customer claims and complaints processes;
2. Any temporary corrections that are implemented to mitigate the effect of the Non-conformity (e.g. refund, credit, upgrade, etc.)
3. The identification, segregation and replacement of the service
4. Equipment, service providers and environment.
This will enable you to judge whether the control of such non-conforming services are effective. In such situations the quality management system should have provisions to capture data on the non-conformities and to feedback information, at the appropriate management level, for the effective definition and implementation of corrective actions. Evidence will need to be sought to justify effective implementation of these techniques.
Join our mailing list to receive upcoming posts: http://www.isoqar.co.za/